I. Definition and Principle of Five-Hole Probes
The five-hole probe is a precision instrument used for measuring three-dimensional flow parameters. It senses the pressure changes in the flow field by opening five small holes at the head of the probe and using these holes. When the fluid flows through the probe, the pressure felt by different holes will vary due to factors such as the incoming flow Angle and speed of the fluid. By precisely measuring the pressure values at these five holes and combining the corresponding calibration data and interpolation algorithms, the precise measurement values of aerodynamic parameters such as airflow velocity and incoming flow Angle in the spatial flow field within a certain range can be calculated.
Ii. The Importance of Five-Hole Exploration
2.1 Accurately obtain flow field information
In complex flow field environments, such as the air flow around an aircraft and the gas flow inside an engine, parameters like the velocity and direction of the fluid are constantly changing. The five-hole probe can directly measure these three-dimensional flow parameters, providing researchers and engineers with detailed flow field information and helping them gain a deeper understanding of the movement laws of fluids.
2.2 Optimize system design and performance
In the aerospace field, by using a five-hole probe to measure the flow field around an aircraft wing, one can understand situations such as airflow separation and vortex formation, thereby optimizing the wing design, enhancing the aircraft's lift and reducing drag. In energy engineering, for equipment such as gas turbines and steam turbines, five-hole probes can measure the flow field within the blade channels, providing data support for improving blade shapes and optimizing equipment performance.
2.3 Verify the numerical simulation results
In the research of fluid mechanics, numerical simulation is a commonly used method. However, the accuracy of the numerical simulation results needs to be verified through experimental measurements. As a reliable experimental measurement tool, the five-hole probe can provide actual flow field data, which can be compared with the numerical simulation results to evaluate the accuracy of the simulation and correct and improve the simulation model.
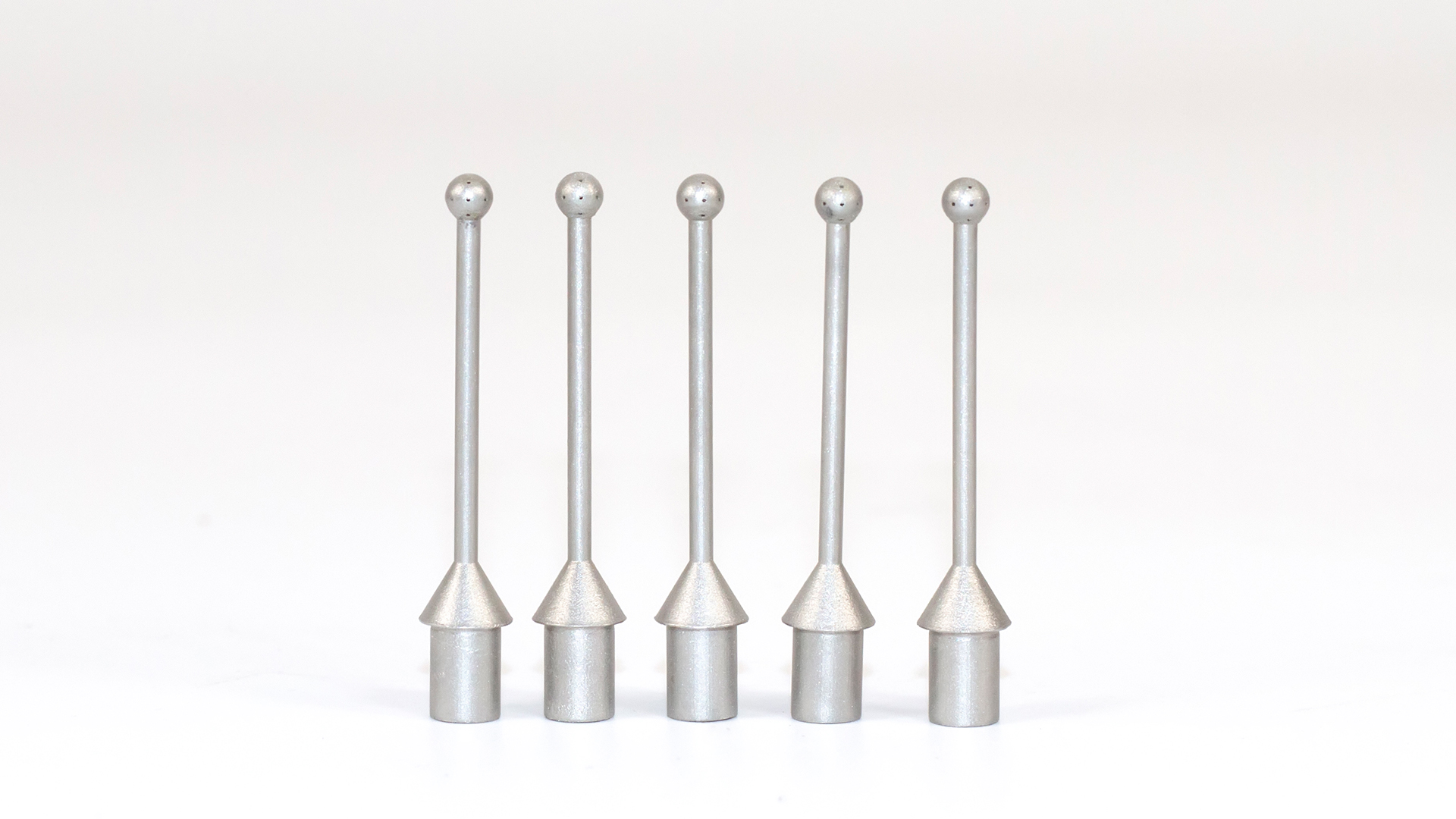
Iii. Analysis of the Number of five-hole Probes
3.1 Measurement Function
The five-hole probe is mainly used for three-dimensional flow parameter measurement and can precisely measure aerodynamic parameters such as airflow velocity and incoming flow Angle within a certain range of spatial flow fields. This enables it to adapt to flow field environments of different complexities and provides key data for various research and engineering applications.
3.2 Probe Types
Common head shapes of five-hole probes include L-shaped, straight, comb-shaped, rake-shaped, and mesh-shaped, etc. Different types of probes are suitable for different measurement scenarios. For example, the L-shaped probe might be more suitable for measurement in a limited space; The rake-shaped probe can simultaneously measure the parameters of multiple position points, improving the measurement efficiency.
3.3 Measuring Object
It can measure the flow field around complex shapes such as spheres, cones and cones. This feature enables the five-hole probe to accurately obtain flow field information when dealing with objects with complex geometries.
3.4 Measurement Accuracy
Its measurement Angle accuracy can reach ≤±45°, which indicates that the five-hole probe has high accuracy when measuring the incoming flow Angle. In many applications with high requirements for Angle measurement, such as the research on attitude control of aircraft, this accuracy can meet the actual needs.
3.5 Mach number range
The applicable Mach number range is Ma: 0 to 2. This means that the five-hole probe can be used for measurement in flow fields ranging from low speed to high speed, covering different flow states such as subsonic and transonic, and has a wide range of applications.
3.5 Material Selection
Materials such as stainless steel, high-temperature alloys, titanium alloys, chromium-nickel-iron alloys, and cobalt-chromium alloys are adopted. These materials possess excellent properties such as high-temperature resistance, corrosion resistance and high strength, enabling the five-hole probe to be used in harsh working environments, such as measuring the internal flow field of high-temperature engines.
Iv. Advantages of Windtuner Technology's Customized Production Service for Five-hole Probes
Windtuner Technology's customized production service for five-hole probes can design and manufacture the most suitable five-hole probes based on the specific needs of customers, such as different measurement scenarios, measurement parameter requirements, and working environments. This customized service can not only enhance the accuracy and efficiency of measurement, but also meet the personalized demands in some special application scenarios. For example, for some miniaturized experimental equipment, Windtuner Technology can customize five-hole probes with smaller dimensions and higher precision. For measurements in extreme environments such as high temperatures and high pressures, more suitable materials and processes can be selected to ensure the performance and reliability of the probe.
As an important tool in the field of fluid measurement, the five-hole probe plays a key role in many fields with its precise measurement capability and wide application range. Windtuner Technology's customized production service for five-hole probes provides more professional and personalized solutions for various industries, promoting the development and application of fluid measurement technology. With the continuous advancement of technology, it is believed that the five-hole probe will demonstrate its unique value in more fields.